GC CORE 350
Highest corrosion protection with high throughput rates
GC CORE 350 is an alkaline zinc-nickel alloy process with 12 to 15 % nickel incorporation for the highest corrosion protection requirements. This electrolyte is best suited for high-throughput drum systems. It is also possible to use it in rack machines.
A great advantage results from the small amount of complex-forming active ingredients used. This reduces the formation of unwanted degradation products and allows an easy bath management.
In continuous operation, GC CORE 350 shows high efficiency and convinces thanks to its excellent covering and throwing capabilities.
The zinc-nickel alloy layers deposited by the GC CORE 350 can be easily passivated and exhibit a high corrosion protection even after thermal stress in the passivated state.
GC CORE 400
Highest corrosion protection for zinc-nickel rack materials with high-quality appearance
GC CORE 400 is a zinc-nickel alloy process with 12 to 15 % nickel incorporation specially developed for rack systems.
The deposited layers have a semi-gloss to a high-gloss surface.
The electrolyte is insensitive to high current densities and has excellent coverage and layer thickness distribution.
The use of GC CORE 400 can be done with both inert anodes and with membrane anodes. When using membrane anodes, highest operational reliability is achieved with consistently high efficiency. The constant quality thereby enables a high throughput. Another advantage results from the reduced disposal costs since the electrolyte does not age due to anodic degradation products. The bath management is considerably simplified by the stable coating process.
The zinc-nickel alloy layers deposited by the GC CORE 400 can be easily passivated and exhibit high corrosion protection values even after thermal stress in the passivated state.
GC CORE 500
Zinc-nickel electrolyte, efficient and high gloss
High-gloss zinc-nickel layers can be deposited with this electrolyte. A newly developed system of brighteners and wetting agents allows a constant high clouding point with low consumption. The high level of operational reliability achieved enables efficient production.
Thanks to the combination of high depth spreading capability and high firing resistance, the GC CORE 500 is suitable for use in drum and rack systems.
As GC CORE 500 uses a lower amount of complexing agents compared to conventional alkaline zinc-nickel processes, a simplified waste-water treatment is possible.
The layers deposited by the electrolyte can be easily passivated and exhibit high corrosion protection values even after thermal stress in the passivated state.
All additives are free of chlorinated aromatic compounds (AOX).
Coating parameters
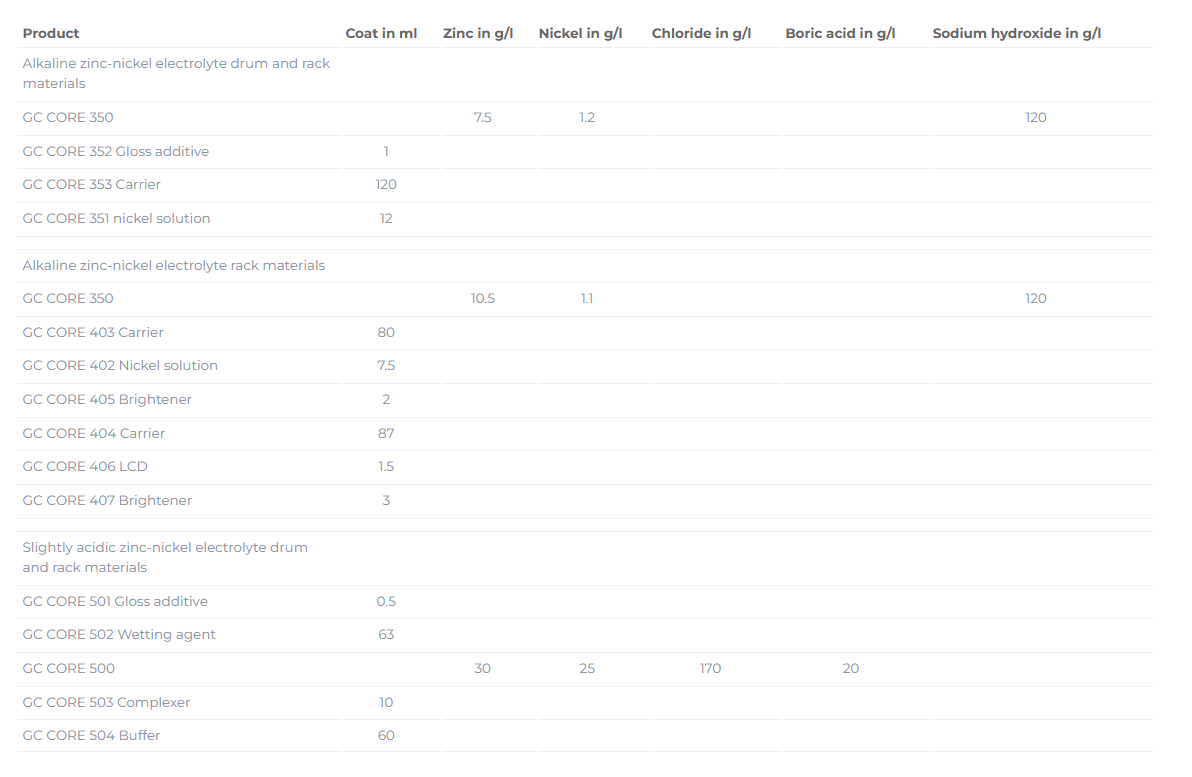